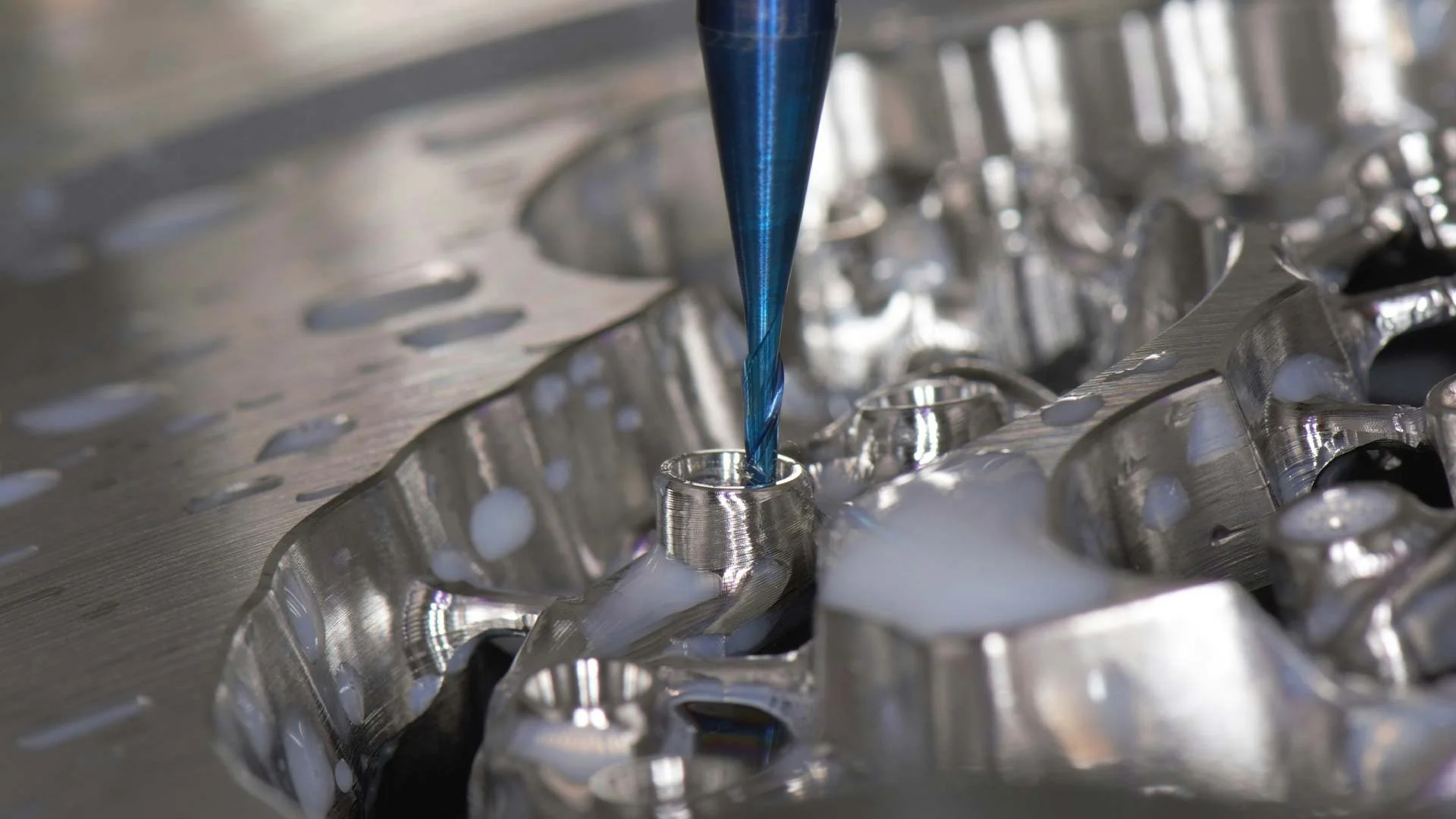
Product features
Here you can see examples of some of the most important features in our products. For further information - contact us and book a demonstration.
ShopFloor features
Adapting the Shop Floor system to your needs
The ShopFloor solution is built to flexibly accommodate your specific requirements.
Its extensive configuration options allow you to tailor the system to your unique operational processes and use cases.
Can I change the production order execution sequence?
Orders can be expedited or postponed from the predefined date sequence according to the planner's preferences.
Shop floor multi-resource job assignment
Reduce lead time by assigning multiple resources for parallel execution as needed.
Flexibility in resource allocation is a powerful tool for planners.
Job execution across multiple production orders
In modern manufacturing, similar processes from different production orders are often grouped together — such as laser cutting, assembly, and more.
Controlling production capacity
It is crucial for the planner to have visibility into the current and future load on a machine or work center.
ShopFloor Planning provides the necessary overviews to support this.
Digital order processing information
The operator has all necessary instructions, process sheets, tooling, and quality information available on the display — everything needed is right at hand.
Planner shop floor control
The ShopFloor system is split into two areas: the planner's workspace and the operator's execution area — both fully integrated.
CadConnect features
Avoid double keying your CAD data
Avoid duplicating data in Business Central that already exists in the CAD system.
Instead, use electronic transfer and automated creation.
Make complex sales qouting work made easier
Handle sales quotes with complete product specifications without entering data into Business Central until the quote is converted into a confirmed sales order.
Create variant products based on existing products
CadConnect allows for using Business Central product data to create similar variant products.
Work with product versions the Business Central way
CadConnect supports bill of materials product versioning including item versioning.
ItemPlanning features
The intuitive way to see and work with expected item inventory
A complete overview of item availability including simulation facilities and shortage impact on sales orders.
The easy way to control shortage challenges
Full item shortage overview of production/assembly and sales orders. And the option that shortages can be actioned right away.
Answer the "When can we deliver" questions
Supports non-stocked produced Bill of Material items.
Displays two key dates: a materials completion date—when shortages are resolved—and a finished production due date—when the item can be produced.
quick overview to identify items that require the planner's attention
The ItemPlanning – Critical Items function evaluates potential understocking and overstocking scenarios, both in the near term and further into the future.
MakeToOrder features
Don't stay stuck—adjust the due dates on your project production orders
NAVEKSA Make-to-Order eliminates the restriction on changing due dates for active project production order lines—a crucial function when plans change.